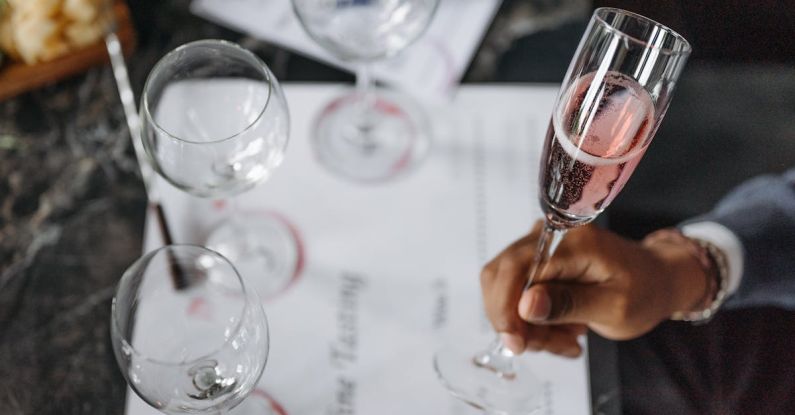
Robotic technology has made significant advancements in recent years, with applications ranging from industrial automation to entertainment. One key aspect of ensuring the optimal performance of a robot is calibration. Calibration is the process of adjusting a robot’s settings to ensure accuracy and precision in its movements and functions. However, even with the most advanced robotic systems, calibration issues can arise, affecting the robot’s performance. In this article, we will explore some of the common calibration issues that can impact RC robots and how to address them effectively.
### Drifting
One of the most common calibration issues encountered in RC robots is drifting. Drifting occurs when a robot does not maintain its intended position or orientation, leading to inaccuracies in its movements. This issue can be particularly problematic in tasks that require precise positioning, such as pick-and-place operations or navigation tasks.
### Solution:
To address drifting in RC robots, it is essential to recalibrate the robot’s sensors regularly. Sensors such as gyroscopes and accelerometers play a crucial role in determining the robot’s position and orientation. By calibrating these sensors correctly and ensuring they are free from any interference, drifting issues can be minimized or eliminated.
### Inconsistent Movement
Another common calibration issue in RC robots is inconsistent movement. This can manifest as jerky or irregular motions, hindering the robot’s ability to perform tasks smoothly and accurately. Inconsistent movement can be caused by inaccuracies in the robot’s motor control system or improper calibration of its motion parameters.
### Solution:
To address inconsistent movement, it is important to fine-tune the robot’s motor control settings and motion parameters. This may involve adjusting parameters such as acceleration, deceleration, and speed to ensure smooth and consistent movement. Additionally, regular maintenance of the robot’s mechanical components, such as motors and gears, can help prevent issues that may lead to inconsistent movement.
### Sensor Calibration Errors
Sensor calibration errors can also pose significant challenges in RC robots. These errors can result in inaccurate data readings, leading to faulty decision-making by the robot’s control system. Sensor calibration errors can be caused by various factors, including environmental conditions, sensor degradation, or improper calibration procedures.
### Solution:
To address sensor calibration errors, it is crucial to conduct regular calibration checks on all sensors used by the robot. This includes verifying the accuracy of sensor readings under different operating conditions and calibrating sensors as needed. Additionally, ensuring proper sensor placement and protection from external factors can help minimize calibration errors and improve the robot’s overall performance.
### Communication Interference
Communication interference is another common calibration issue that can impact RC robots. This issue occurs when the robot’s communication system, such as radio frequency (RF) or Bluetooth, experiences disruptions or signal loss, leading to a loss of control or data transmission errors.
### Solution:
To address communication interference, it is important to identify and eliminate sources of interference in the robot’s operating environment. This may involve changing the operating frequency, using shielding materials, or optimizing the communication protocols to minimize signal disruptions. Regularly checking and maintaining the robot’s communication system can help prevent issues related to communication interference.
### Conclusion
Calibration plays a crucial role in ensuring the optimal performance of RC robots. By addressing common calibration issues such as drifting, inconsistent movement, sensor calibration errors, and communication interference, robot operators can enhance the accuracy, precision, and reliability of their robotic systems. Regular maintenance, calibration checks, and troubleshooting procedures are essential practices to mitigate calibration issues and maximize the efficiency of RC robots in various applications.